- Clogged print heads
- Ink adhesion problems
- Film jams
- Inconsistent colors
- Poor washability
- Printer communication errors
- Overheating
- Software issues
- Ink leakage
(一) Clogged print heads
One of the most common problems with DTF printers is clogged print heads. This problem can cause stripes or incomplete printing, thus affecting the design quality.
- Prevention: Regular maintenance is the key. Make sure to clean the DTF printer daily, especially after frequent use. Utilize the cleaning function available on most DTF printers.
- Solution: If you notice stripes or missing colors, run a print – head cleaning cycle. If the problem persists, manually clean the print head with a lint – free cloth and a cleaning solution. For severe clogs, professional service may be required.
(二) Ink adhesion problems
Another common problem is poor ink adhesion, which can cause DTF prints to peel or crack after application.
- Prevention: Ensure that you are using high – quality DTF printing inks and films. Low – quality materials can lead to poor results.
- Solution: Check the temperature and pressure settings on the heat – press machine. Incorrect settings can cause the ink to not bond properly to the fabric. Adjust these settings as needed according to the manufacturer’s recommendations.
(三) Film jams
Film jams are a troublesome problem that can stop your printing process and even damage your DTF machine.
- Prevention: Always use the correct type of film for your DTF printer. Make sure the film is loaded correctly and that the printer rollers are clean and functioning properly.
- Solution: If a jam occurs, carefully remove the jammed film to avoid damaging the printer. Check for any obstructions or debris in the paper feed path and clean as needed.
(四) Inconsistent colors
Achieving consistent color output is crucial for professional – quality DTF printing. Inconsistent colors can be caused by various factors, including ink quality and printer settings.
- Prevention: Regularly calibrate your DTF printer and use ICC profiles that are suitable for your specific printer and ink combination.
- Solution: If there are inconsistent colors, perform a nozzle check to ensure that all colors are printing correctly. If the problem persists, adjust the color settings in the RIP software and consider switching to higher – quality inks.
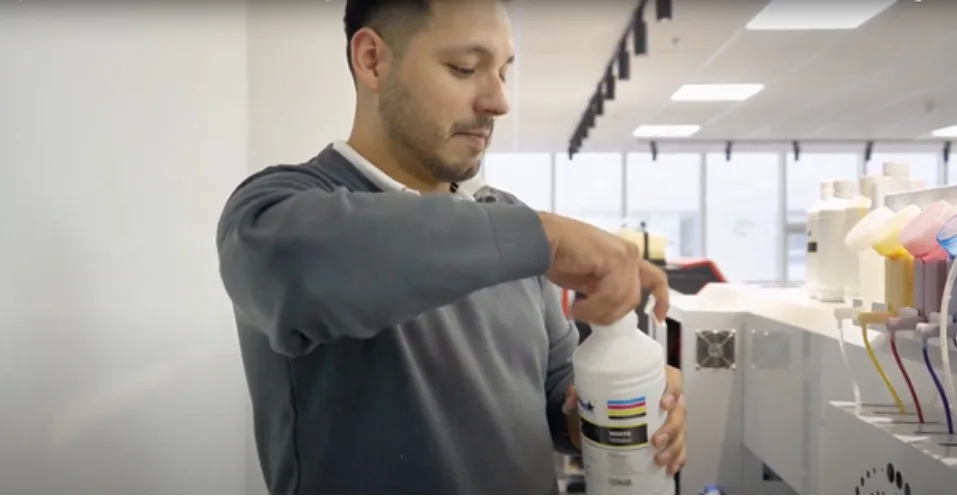
(五) Poor washability
Poor washability is a significant problem, especially for garments that need to be washed frequently. Prints that fade or deteriorate after washing can damage your reputation and customer satisfaction.
- Prevention: Use durable, high – quality inks and films. Use a heat – press machine to follow the recommended curing process.
- Solution: If there are washability problems, confirm that the temperature, pressure, and time settings used during the heat – transfer process are correct. Ensure that the fabric has been properly pre – treated to improve ink adhesion.
(六) Printer communication errors
Communication errors between your computer and DTF printer can interrupt your workflow and cause delays.
- Prevention: Ensure that all software and firmware are up – to – date. Use high – quality, compatible USB or network cables.
- Solution: Restart the printer and the computer. Check all cable connections and replace any faulty cables. If the problem persists, consult the printer manual or contact technical support.
(七) Overheating
Overheating can damage your DTF printer and affect printing quality. This problem usually results from long – term use or poor ventilation.
- Prevention: Ensure that the printer is placed in a well – ventilated area and avoid overloading caused by continuous printing jobs.
- Solution: If the printer overheats, turn it off and let it cool. Check for any obstructions in the ventilation and remove dust or debris from the cooling fan.
(八) Software issues
Software malfunctions or incompatibilities can hinder your printing operations, especially when you are using outdated or unsupported software.
- Prevention: Regularly update your printing software and drivers to the latest versions provided by the manufacturer.
- Solution: If there are software problems, reinstall the software or try using another computer. If necessary, contact customer support for help.
(九) Ink leakage
Ink leakage can cause trouble and may damage your printer and workspace. This problem usually results from improper installation or maintenance.
- Maintenance: Always keep an eye on your DTF printer to see if there are any signs of it. Ensure that the cartridges and ink tanks are properly placed and sealed.
- Solution: If there is ink leakage, immediately clean the affected area and check the printer for any damage. Replace any faulty components and ensure that all connections are secure.
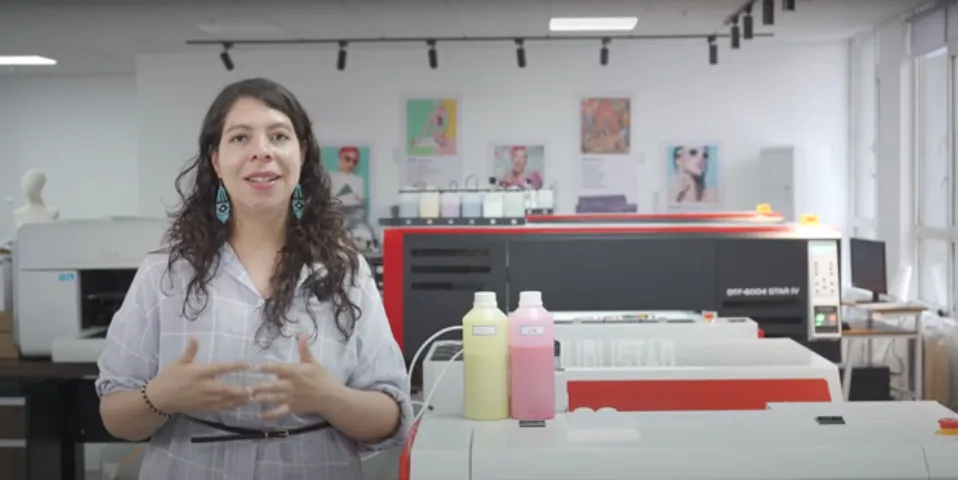
Conclusion
If you know how to solve the problems related to DTF printers, this will improve the quality of print output and user experience. By following these guidelines, you will avoid many problems with the equipment and ensure the smooth operation of the DTF printer.
If you wish to upgrade your equipment or seek more help, visit our product website and enhance your printing capabilities.