DTF heat transfer film is a substrate specially designed for white ink heat transfer printing. It uses the heat transfer principle to transfer patterns onto fabrics or other materials. It can be said that the heat transfer film directly determines the transfer quality of white ink heat transfer printing.
The white ink heat transfer printing technology has been developed for decades. The process and effect are constantly updated. Naturally, many different types of DTF heat transfer films have emerged on the market. Currently, common ones are cold peel film, hot peel film, and instant peel film.
Facing a wide variety of heat transfer films, many customers are puzzled: What exactly is a heat transfer film? What are the differences between these heat transfer films? Which one should be chosen to avoid pitfalls? Follow AGP, a professional manufacturer of white ink heat transfer printers, and find the answers in the text!
I. What is a heat transfer film?
Heat transfer film is a special PET film with a coating. It usually consists of six layers: base layer, release layer, adhesive layer, printing layer, protective layer, and antistatic layer. It is used in the transfer process of DTF white ink heat transfer printing.
From the white ink heat transfer printing process, we can see that the last step of the entire heat transfer printing process is to peel off the heat transfer film, leaving the pattern on the transfer object. The hot peel film, cold peel film, and instant peel film we are going to understand today are heat transfer films distinguished by different peeling times.
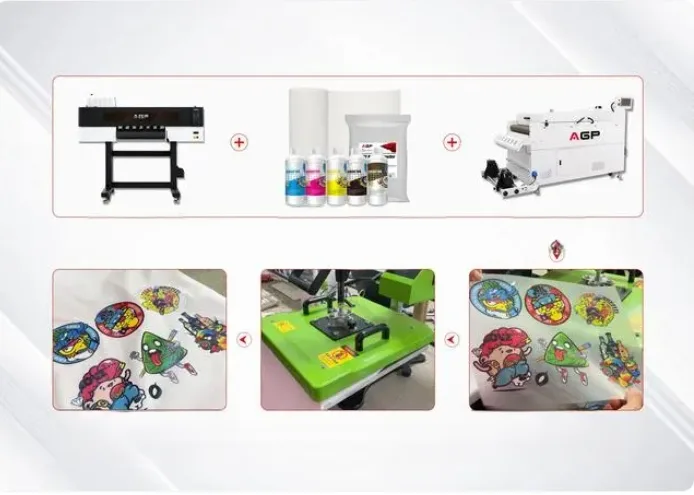
1.1 What is hot peel film?
Hot peel film is a PET heat transfer film that can be peeled off immediately after the heat transfer is completed while the heat transfer film is not yet cooled (usually within 10 seconds after pressing, when the ambient temperature is 35°C or the film surface temperature is greater than 100°C), without waiting for it to cool.
Characteristics: Using hot peel film can save the time waiting for the heat transfer film to cool and improve the printing efficiency of mass production. However, if not peeled off in time, the cooled glue may stick to the clothing, causing difficulties in peeling off and even problems such as pattern residue. Generally speaking, hot peel film has more strict requirements on pressing time, temperature, and pressure.
1.2 What is cold peel film?
Cold peel film is a PET heat transfer film that needs to wait for the film to cool to a certain temperature (usually waiting for 30 seconds, or when the film surface temperature is lower than 55°C) before it can be easily peeled off after the heat transfer is completed.
Characteristics: Cold peel film requires a certain cooling time, but the product stability is better, and the color effect is matte. Cold peel film is very suitable for special fabrics (such as coated cloth, canvas, flannel and other rough-textured fabrics). Because after such fabrics are hot-pressed, using cold peel film gives sufficient time to restore their flatness.
1.3 What is instant peel film?
Instant peel film can actually be regarded as a supplementary form of hot peel film. It is a PET heat transfer film that can be peeled off almost immediately after pressing.
Characteristics: Due to its fast peeling characteristic, instant peel film may be more suitable for scenarios requiring high efficiency and mass production. However, it has stricter requirements on peeling time and is more difficult to operate.
II. Which is better, hot peel film/cold peel film/instant peel film?
Hot peel film, cold peel film, and instant peel film each have their own advantages and disadvantages and are suitable for different types of production and printing needs.
Generally speaking, DTF hot peel film and instant peel film are more suitable for mass production of ordinary fabric clothing such as cotton T-shirts.
Note: Hot peel film has more detailed requirements on pressing time, temperature, and pressure. Adjust the temperature to between 140-160 degrees, the pressure to 4-5KG, and press for 8-10 seconds, then it can be easily peeled off.
Compared with DTF hot peel film, DTF cold peel film has stronger stability (the main component of cold peel film is silicon. Compared with wax, the main component of hot peel film, silicon is easier to melt and apply). It is suitable for more fine and complex pattern lines. It is recommended to control the pressing temperature at 150-170°C and the time at 10-20 seconds. Wait for the film surface to cool before peeling off.
Each DTF heat transfer film has its own advantages. You can choose the heat transfer film that suits your business according to your actual needs. After all, there is no perfect product. The one that suits you is the best!
Special reminder: Different brands and types of PET heat transfer films may have slight differences. Therefore, be sure to read the product instructions carefully before using. It is highly recommended that you conduct a separate new product test before producing large quantities to ensure the final heat transfer effect.
III. How to choose high-quality heat transfer film?
- High ink loading capacity
DTF heat transfer films with inferior ink-absorbing or water-absorbing layers may experience problems such as ink leakage, fading, or water seepage during the printing process.
- High coating quality
The surface of DTF heat transfer film has a special coating. If the coating is uneven or contains impurities, it will directly affect the printing effect. Therefore, it is necessary to observe whether the surface coating is uniform and fine.
- No powder adhesion
Some heat transfer films may have residual hot melt powder on the pattern edges after printing and ironing, affecting the aesthetics of the heat transfer product. Please choose a high-quality heat transfer film to ensure that the printed pattern edges are clean and free of residue.
- Easy to peel off
High-quality DTF film can be easily peeled off after pressing to ensure the stability and integrity of the transferred pattern.
- High temperature resistance
The hot melt powder only starts to melt at 80°C. Therefore, DTF heat transfer film must be high temperature resistant. It is recommended that you select a test temperature of 120°C. If the PET heat transfer film does not turn yellow or wrinkle, it can be judged as being of good quality.
If you have any questions, please feel free to contact us. Looking forward to discussing the development of DTF white ink heat transfer printing technology with you and opening up more possibilities!